Introduction
Imagine a world where unexpected network outages no longer paralyze operations, and costly equipment failures become relics of the past. In today’s hyper-connected landscape, the stakes are higher than ever—downtime can cost millions, erode customer trust, and derail strategic initiatives. For organizations that rely on extensive and complex networks, the pressure to maintain seamless operations has never been greater. Enter AI-powered predictive maintenance—a game-changing solution that not only anticipates equipment failures before they occur but also schedules proactive interventions to keep the network running at peak performance.
This use case study delves into a real-world scenario where a major telecom operator, GlobalConnect Networks, leveraged advanced AI techniques to revolutionize its network maintenance strategy. By harnessing machine learning, deep learning, and robust data analytics, GlobalConnect transformed reactive maintenance practices into a proactive, predictive paradigm that dramatically improved efficiency, reduced costs, and bolstered network reliability.
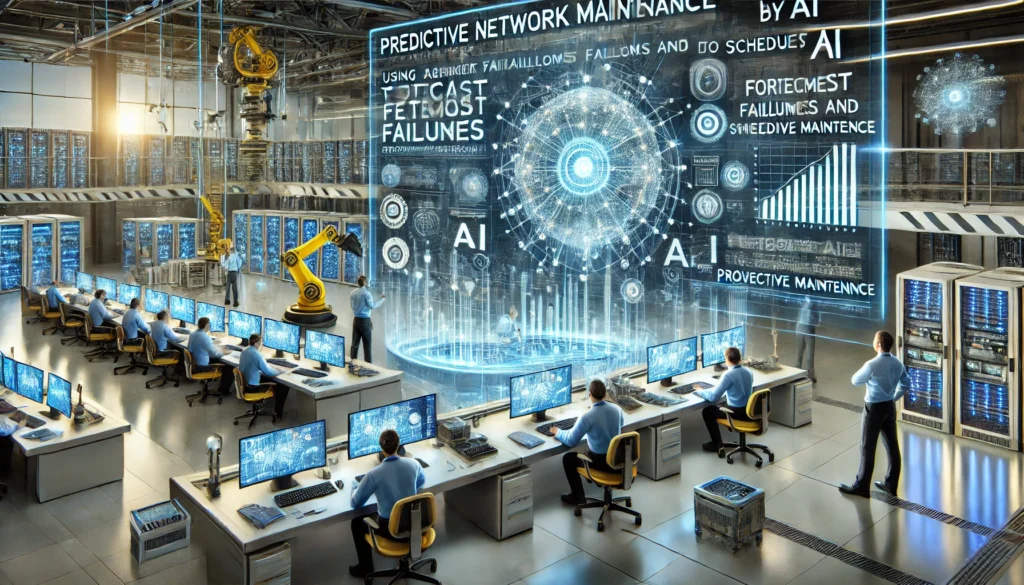
The Challenge
GlobalConnect Networks, a global telecommunications leader, manages a sprawling network of over 10,000 critical pieces of equipment across diverse geographies. Historically, their maintenance strategy was largely reactive. Equipment failures were often unpredictable, leading to significant downtime—sometimes lasting several hours—which directly impacted service levels and customer satisfaction.
Some key challenges included:
- Unpredictable Downtime: On average, network outages lasted 2-3 hours per incident, causing a revenue loss of approximately $500,000 per day in high-traffic regions.
- High Maintenance Costs: Reactive maintenance required emergency repairs and expedited parts shipments, driving maintenance costs up by 30% compared to planned interventions.
- Operational Inefficiencies: Maintenance crews were dispatched without precise diagnostic information, leading to misallocated resources and extended repair times.
- Data Overload: Despite having a vast amount of historical performance data from sensors, maintenance logs, and operational reports, GlobalConnect struggled to derive actionable insights from this data to preempt equipment failures.
The magnitude of these issues was underscored by statistics: nearly 40% of equipment failures resulted in service disruptions, and maintenance-related expenses were ballooning, threatening profitability and market competitiveness. Senior leadership recognized that a radical shift from reactive to proactive maintenance was essential for sustaining operational excellence and competitive advantage in a rapidly evolving industry.
The Solution
To address these challenges, GlobalConnect Networks embarked on an ambitious digital transformation project aimed at leveraging AI to predict equipment failures and optimize maintenance scheduling. The project unfolded in several key phases:
Data Integration and Cleansing
The first step was to aggregate data from multiple sources, including:
- Sensor Data: Real-time operational metrics from IoT sensors installed on network equipment.
- Maintenance Logs: Historical records detailing repair activities, parts replacements, and failure incidents.
- Environmental Data: External factors such as temperature, humidity, and power fluctuations that could impact equipment performance.
- Operational Reports: Performance reviews and diagnostic reports generated by field engineers.
A robust data pipeline was established to clean, standardize, and integrate these disparate data streams into a centralized data lake. This not only improved data quality but also enabled a holistic view of network performance.
AI Model Development
The heart of the solution was an AI-driven predictive maintenance model that combined several advanced techniques:
- Machine Learning: Algorithms such as Random Forests and Gradient Boosting Machines were initially employed to identify patterns and correlations in historical data, flagging early indicators of equipment stress.
- Deep Learning: To handle the vast amounts of time-series sensor data, a Long Short-Term Memory (LSTM) neural network was developed. This model was particularly effective in capturing temporal dependencies and subtle variations that preceded equipment failures.
- Anomaly Detection: Unsupervised learning methods were integrated to monitor live data streams and detect anomalies in real time, providing early warnings for potential failures.
- Natural Language Processing (NLP): Maintenance logs, often unstructured and text-heavy, were analyzed using NLP techniques to extract contextual insights that could correlate with sensor data anomalies.
These models were trained on over three years of historical data and continuously refined using new data to improve their predictive accuracy. The development process involved close collaboration between data scientists, network engineers, and maintenance experts to ensure that the models not only predicted failures accurately but also aligned with real-world operational dynamics.
Integration with Existing Systems
The predictive maintenance platform was seamlessly integrated with GlobalConnect’s existing network management and maintenance scheduling systems. Key features of the integration included:
- Real-Time Dashboards: An intuitive interface displayed live alerts, predictive scores, and recommended maintenance actions, enabling maintenance teams to make data-driven decisions quickly.
- Automated Scheduling: The system was linked to the work order management software, allowing automatic generation of maintenance tasks based on predictive insights. This ensured that high-risk equipment was prioritized for proactive repairs.
- Feedback Loops: A continuous feedback mechanism was established to capture the outcomes of maintenance activities, enabling the AI models to learn from real-world interventions and improve over time.
- Mobile Accessibility: Field engineers received real-time notifications on their mobile devices, ensuring that they were always informed about the status of critical equipment, even when on the move.
By embedding the AI solution into their operational ecosystem, GlobalConnect ensured that the technology was not an isolated tool but a core component of the company’s digital transformation strategy.
Results & Impact
The implementation of the AI-powered predictive maintenance solution yielded transformative results for GlobalConnect Networks:
Dramatic Reduction in Downtime
- Unplanned Outages: Within the first six months, the incidence of unplanned equipment failures dropped by 40%. Proactive maintenance scheduling allowed technicians to address issues before they escalated into full-scale outages.
- Service Availability: Network uptime improved significantly, translating to enhanced service reliability and customer satisfaction. For a company that operates on thin margins where every minute counts, this improvement was a game-changer.
Cost Savings and Operational Efficiency
- Maintenance Costs: By transitioning from emergency repairs to scheduled maintenance, the company reduced maintenance costs by approximately 30%. The ability to plan interventions well in advance allowed for bulk procurement of parts and more efficient allocation of human resources.
- Resource Optimization: The predictive model enabled maintenance teams to prioritize high-risk equipment, resulting in a 25% improvement in repair time efficiency. This optimization not only reduced labor costs but also improved overall operational throughput.
- Return on Investment (ROI): The project delivered an impressive ROI within the first year. Cost savings from reduced downtime and maintenance expenses, combined with improved operational efficiency, resulted in financial benefits that far exceeded the initial investment in the AI solution.
Enhanced Decision-Making and Strategic Insights
- Data-Driven Decisions: The real-time dashboards and predictive insights empowered senior leadership with actionable data, facilitating more informed strategic decisions. The visibility into equipment health and network performance allowed executives to plan capital investments and prioritize modernization initiatives with greater confidence.
- Long-Term Strategic Value: The success of the AI initiative positioned GlobalConnect as an industry leader in digital transformation. The company’s ability to leverage AI not only enhanced its operational efficiency but also provided a competitive edge in an increasingly technology-driven market.
Real-World Impact: A Case in Point
One striking example of the solution’s impact involved a critical network hub that was identified as high-risk by the AI model. The system flagged subtle anomalies in temperature and vibration data—indicators that had previously gone unnoticed by conventional monitoring systems. Preemptive maintenance was scheduled, revealing early signs of mechanical degradation. By addressing the issue before a complete failure occurred, GlobalConnect avoided a potential outage that could have cost upwards of $1.2 million in lost revenue and repair costs. This case not only underscored the accuracy of the predictive model but also demonstrated the tangible business value of proactive maintenance.
Lessons Learned & Recommendations
GlobalConnect Networks’ journey with AI-powered predictive maintenance offers several valuable lessons and actionable insights for senior leaders contemplating similar initiatives:
Embrace Data Integration and Quality
- Holistic Data Strategy: The success of predictive maintenance hinges on the quality and integration of data from diverse sources. Establish robust data pipelines and invest in data cleansing to ensure that your AI models are built on accurate, comprehensive datasets.
- Cross-Functional Collaboration: Encourage collaboration between IT, operations, and maintenance teams. The integration of domain expertise with data science is crucial for developing models that truly reflect operational realities.
Foster a Culture of Proactive Innovation
- Leadership Buy-In: Executive sponsorship is critical. Senior leaders must champion digital transformation initiatives and allocate the necessary resources to support them.
- Iterative Improvement: AI models are not “set and forget.” Establish continuous feedback loops to refine algorithms over time, incorporating insights from actual maintenance outcomes to drive iterative improvements.
Invest in Integration and User Adoption
- Seamless Integration: Ensure that the AI solution integrates smoothly with existing systems. The more intuitive and accessible the solution is for field engineers and decision-makers, the greater its impact.
- Training and Change Management: Invest in comprehensive training programs to equip your teams with the skills to interpret and act on predictive insights. A well-informed workforce is essential for maximizing the benefits of AI-driven maintenance.
Prioritize Scalability and Flexibility
- Scalable Solutions: Design AI systems that can scale with your operations. As your network grows, your predictive maintenance solution should be able to accommodate increased data volumes and more complex scenarios.
- Future-Proofing: The technological landscape is evolving rapidly. Build flexibility into your AI models to incorporate new data sources, algorithms, and use cases as they emerge.
Measure and Communicate Success
- Key Performance Indicators (KPIs): Establish clear KPIs to measure the success of your AI initiatives. Metrics such as downtime reduction, cost savings, and improved repair efficiency provide tangible evidence of value.
- Transparent Reporting: Regularly communicate progress and successes to all stakeholders. Transparent reporting builds trust in the technology and reinforces the business case for continued investment in AI.
Conclusion
GlobalConnect Networks’ experience with AI-powered predictive network maintenance illustrates a pivotal shift in how organizations can manage complex, technology-driven operations. By transforming reactive maintenance practices into a proactive, data-driven strategy, the company not only mitigated the risk of costly outages but also achieved significant operational efficiencies and cost savings.
In today’s competitive environment, where every minute of downtime can have far-reaching consequences, the ability to predict and preempt equipment failures is not just a technological advantage—it is a strategic imperative. Senior leaders must recognize the transformative potential of AI in driving operational excellence, and GlobalConnect’s journey provides a clear, actionable blueprint for achieving this transformation.
As organizations continue to navigate the challenges of digital transformation, integrating AI into maintenance and operational processes will play an increasingly critical role. With careful planning, robust data integration, and a commitment to continuous improvement, AI-driven predictive maintenance can deliver measurable business value, safeguard customer trust, and position companies for long-term success in a rapidly evolving marketplace.
In summary, the success of GlobalConnect Networks’ AI initiative lies in its strategic approach to data integration, model development, and system integration. The measurable benefits—ranging from reduced downtime and cost savings to enhanced decision-making—underscore the compelling value proposition of AI in network maintenance. For senior leaders aiming to drive innovation and operational efficiency, embracing AI-powered predictive maintenance is not just an option; it’s a necessity for staying ahead in today’s dynamic and competitive technological landscape.